Catalytic Reforming Process Fundamentals
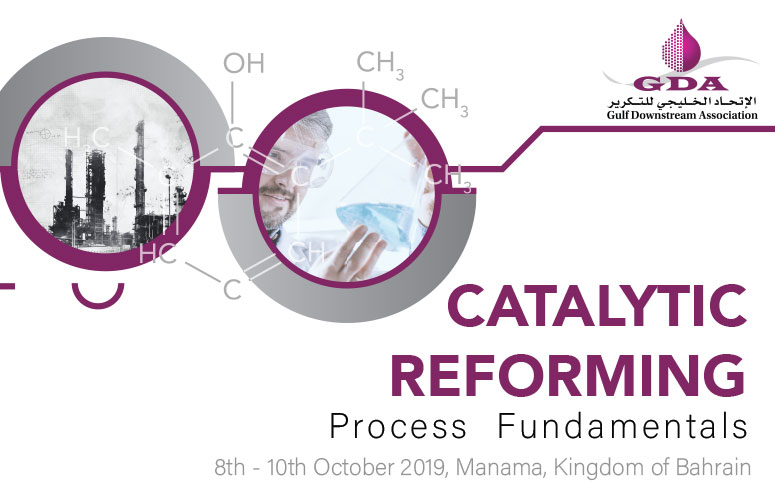
OVERVIEW
The catalytic reforming process is critical to essentially every modern refinery and petrochemical plant. Since the early 1940s, dual function catalysts have been converting lower octane naphtha-range hydrocarbons into aromatics and higher octane blend stock for petrochemicals and gasoline production while producing valuable hydrogen as a by-product. Early on, the associated technology became known as catalytic naphtha reforming to acknowledge that the desired products resulted from molecular rearrangement, reforming, of the reactants without alteration of their carbon number. Numerous improvements in catalyst and process technology have been commercialized over the past seven decades.
This comprehensive course will focus on teaching the fundamentals of catalytic reforming, primarily for semi-regenerative and CCR reformers, and facilitate direct interaction with experts in the field as well your peers responsible for reformer performance in refineries and chemical plants throughout the region. The course is designed as a series of presentations that will provide fundamental understanding of key reforming principles. Mastery of these principles will facilitate maximization of reformer profitability. Each presentation will conclude with a brief quiz, a question and answer session and open discussion to maximize understanding of the key principles which can be grouped into the following general topics:
- Reforming Basics
- Reformer Operations
- Reformer Performance Improvement
- Reformer Monitoring
- Reformer Troubleshooting
COURSE BENEFITS
Upon successful completion of this training, the participant will be able to:
- Understand how naphtha composition and characteristics impact reformer catalyst performance.
- Understand the desirable reactions that increase reformate octane and the undesirable reactions that reduce reformate yield.
- Understand the major pieces of reformer equipment.
- Understand the catalyst’s acid and metal functions, the need for water-chloride management, the impact of catalyst surface area stability, and the impact of poisons on catalyst performance.
- Understand how process variables impact catalyst activity, stability and yields.
- Understand the basic steps necessary for successful catalyst regeneration and identify critical junctures that can quickly compromise catalyst regeneration success and concomitant performance quality.
- Understand the basics of reformer performance monitoring, forward performance projection and catalyst sample analysis.
- Understand how to troubleshoot reformer performance issues.
- Understand how to improve reformer performance through optimum catalyst selection and loading.
WHO SHOULD ATTEND?
Process Engineers and Operators working in reforming that want to gain more in-depth knowledge. Technologists, Supervisors and Managers working in Research, Technical and Planning positions looking to gain general knowledge.
Date: | 08th-10th October 2019 (1 Day) | |
Time: | 08:00-16:00 Hrs. | |
Venue: | Wyndham Grand Manama Hotel, Kingdom of Bahrain (https://goo.gl/maps/TZyyAdz9mDH2) |
|
Fee: | USD 3,250 per participant (Special for GDA Members only) | |
Reformer Bascis |
Reformer Operations Reformer Monitoring |
Reformer Troubleshooting Reformer Performance Improvement |
---|---|---|
Naphtha Block & Reforming Introduction | Process Variables | Troubleshooting Performance Issues |
Birth of Reforming | Water-Chloride Management | Feed-Effluent Exchanger Leak |
Naphtha Composition & Characteristics | Regeneration Overview | Metal Dusting |
Reaction Chemistry | Material Balance Overview | Green Oil Formation |
Modern Process Technology | Performance Normalization & Forward Projection | Excessive CCR Catalyst Attrition |
Catalyst Composition & Function | ConnectIn™ | Catalyst Maldistribution |
Catalyst poisions | Analytical Tools | Catalyst Innovation |
Catalyst Surface Area Stability | Catalyst Analysis
|
|
Catalyst Loading
|
MEET YOUR TRAINER
Bill Kostka started his professional career in 1981 as a research engineer at Mobil Research and Development Corporation in Paulsboro, New Jersey where he acquired extensive R&D, pilot plant testing and technical support experience in a variety of programs with major emphasis on catalytic naphtha reforming and isomerization. In 2000, he became part of ExxonMobil Research and Engineering Company in Fairfax, VA where he progressed through a series of leadership assignments in reforming and isomerization before retiring in early 2013 as Commercial Technology Leader for these two technologies. He joined Axens North America in late 2013 as a Senior Technology Advisor.
Bill holds a PhD in Chemical Engineering from Purdue University.
*************
Jad Abou Charbine is the Technical Services Manager at Axens Middle East, leading a team of highly skilled engineers ensuring technical support for the refineries in the GCC. He joined Axens in 2010 and served as process engineer and start up engineer before being appointed to his current position. Jad is specialized in catalytic reforming as well as aromatics paraxylene production technologies and has been in charge of design, training, commissioning and start up.
Jad holds a process engineering degree from Université de Technologie de Compiègne (France) and a master degree in energy and processes from the IFP School (France).